Why Custom Lead Screw Nuts Might Be the Answer to Your Problems!
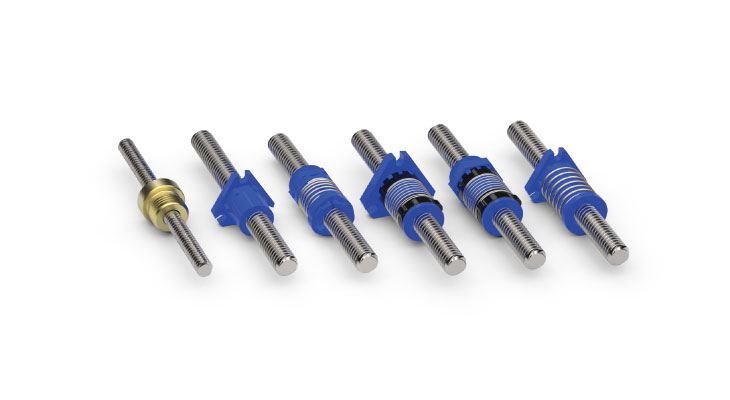
Many factors dictate the performance of a lead screw, including how it is mounted, as we covered in our last article. However, the most crucial factor is pairing the lead screw with the lead screw nut. Don't shy away from designing a custom lead screw because the costs and speed to market are more attractive than ever.
It may sound like we're stating the obvious, but we don't think so. Due to the many advancements in nut design and material variety, it's not such a straightforward decision these days. It's common for some to overlook the impact of the nut after they've selected the lead screw for a particular application. Still, as many motion control applications are becoming more and more sophisticated - notably those in lab automation and medical equipment - the proper pairing of the lead screw and nut is becoming a paramount design decision. A single lead screw may have dozens of nut options, and even those may not suit your particular application.
Yes, there are a variety of standard lead screw nuts available, which offer the perfect choice for most applications (just as standard lead screws are suitable for many applications). But then there's also the option of a custom-engineered lead screw nut to meet the needs of more advanced and sophisticated applications - applications where there's little room for error or applications where the parameters of the overall design require something "outside of the box." How do you know whether or not a standard nut will do the trick or if a custom nut is in your application's best interest?
Here's a look at some of the design variables that you might want to consider during the nut-selection process to help with your decision:
- Temperature constraints: Does the application need to operate within a specific temperature range? Certain custom materials for our custom nuts perform well in high and/or low temperatures.
- Chemical compatibility: How strong is corrosion resistance? Will materials be impacted negatively by the environment the application will be operating in? Certain materials are more corrosion resistant than others.
- Wear: How long does the nut need to last in the particular application? Nuts can be custom engineered to last for extended periods.
- Matching leads: Do all leads in the application have to remain consistent
- Lubricants: It's common for a lead screw nut to require some lubrication, but does your selection need a particular type of lubrication? What about self-lubricated nuts?
- Backlash: Do you need to worry about lash? Should you be considering an anti-backlash assembly?
- Flange: Does a flanged nut or a nut with no flange work better in your application? Can you eliminate another component or simplify the design by choosing a flanged nut?
- Cost: A custom design may initially cost a little more than a standard nut, but that is not always the case. Perhaps it can even reduce the overall cost and complexity by incorporating design elements of other components, thereby eliminating them and their potential failure points. A custom nut may also contribute to lower maintenance costs and failure reduction. How heavily do these factors weigh in the design?
After you've carefully analyzed all of the design variables above, it's time to stack up against standard nuts with custom nuts. Custom nuts don't necessarily have to be advanced or highly complex; in some cases, they can be as simple as a dimensional change or use of a particular type of material or a custom mounting hole pattern. Thread options and specific manufacturing techniques may also be used to fabricate custom nuts. Custom nuts provide engineers with greater design flexibility and thereby allow them to design without being constrained by the parameters of the lead screw assembly.
Helix Custom Lead Screw Nuts
Lead screw nuts can be created in a variety of advanced materials these days. At Helix, we can create custom nut configurations in many types of plastics, including PEEK, polyester, acetal, Torlon, Vespel, PVDF, UHMW, and Ertalyte, to name a few. Many of the nuts mentioned above, such as those manufactured from Torlon, Vespel, and PEEK, are ideal for applications that need to operate in high temperatures. Aside from plastic materials, nuts can also be fabricated from carbon fiber, graphite, glass fibers, and silicone.
As we mentioned earlier, lab automation and medical device design and manufacture are two areas that are playing a significant role in driving lead screw development and innovation. This is primarily due to the requirement for increased precision and demands for a smaller footprint. With that being said, the resulting lead screw assemblies necessary to drive these applications have produced some impressive lead screw nut innovations. Custom nuts have already come a long way - and their design advancements are likely to continue.