Ball Screws vs Lead Screws
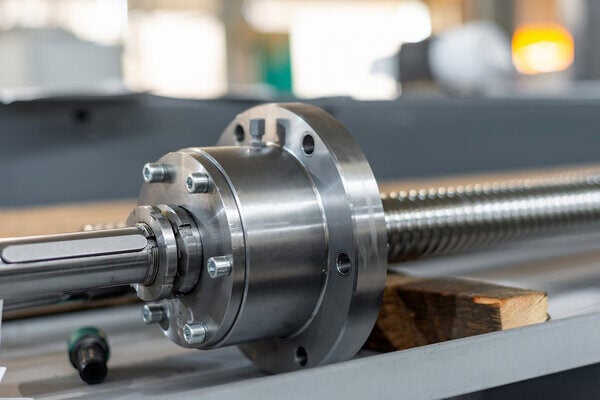
When it comes to linear motion applications, the choice between ball screws and lead screws is essential. Both technologies are well-known in the industry, yet their design, functionality, and performance characteristics differ in ways that can significantly impact your application's efficiency and effectiveness. Understanding these distinctions is important for optimizing your systems, whether aiming for high-speed precision or cost-effective durability.
Revisiting the core differences
One of the main differences between ball screws and lead screws is that ball screws rely on the ball bearings to reduce the friction between the nut and the screw. Lead screws do not. Furthermore, ball screws have a nut and screw that match helical grooves, which enable the ball bearings to re-circulate. Continuously, this component also often has a semi-circular shape, assisting with the spherical ball bearing. On the other hand, lead screws rely on helical threads and a mating nut.
Another significant difference between the two screws is that ball screws perform in a rolling manner. Resulting in the reduction of sliding friction and ensuring that the ball nut produces smooth and highly efficient linear motion alongside the axis of the ball screw. It does all this while making sure the ball screw uses as little friction as possible.
While anatomy and the level of friction produced by these two components are key factors, other differences include backlash, speed, lead accuracy, and efficiency. For clarification, lead screws produce a minimal backlash and drag. This means that the application they are used in will last longer, perform better, and cost less by reducing the requirements the motor will need to perform.
Application-specific considerations
When pertaining to industrial applications, ball screws are typically preferred due to their higher load requirements. They also work well in these types of applications because of their ability to work smoothly, accurately, precisely, continuously, efficiently, and at high speeds.
As for lead screws, the applications in which they excel are smaller or require less duty. Furthermore, OEM applications often use these components due to their unique demands. There are great lead screw calculator tools for defining the best lead screw for your application.
Cost-benefit analysis
While ball screws are typically sold at a considerably higher price than lead screws, they provide different benefits. However, lead screws are often easier to customize. With that being said, Helix Linear Technologies offers customizable options for both ball screw and lead screw nut designs. Our team of experts specializes in crafting both components that will perfectly fit your diverse applications.
Innovations and trends
Recent advancements in linear motion technology are significantly enhancing the performance of ball screws and lead screws through new materials, coatings, and design improvements. Precision manufacturing techniques, such as advanced CNC machining, are also playing an essential role in tightening tolerances and improving accuracy in ball screws.
Additionally, hybrid systems that combine the strengths of both ball screws and lead screws are emerging, offering an optimal balance of efficiency and load-bearing capabilities—particularly in applications where traditional designs may fall short. These innovations are expanding the possibilities, making linear motion systems more efficient, reliable, and customizable.
Conclusion
Choosing between ball screws and lead screws is vital for optimizing your linear motion application. Ball screws offer high-speed precision with minimal friction, while lead screws provide cost-effective durability with low backlash. Understanding these differences and recent innovations will help you choose the best option to meet your specific performance needs and application requirements.