Debunking Acme Lead Screw Misconceptions in Linear Motion Applications
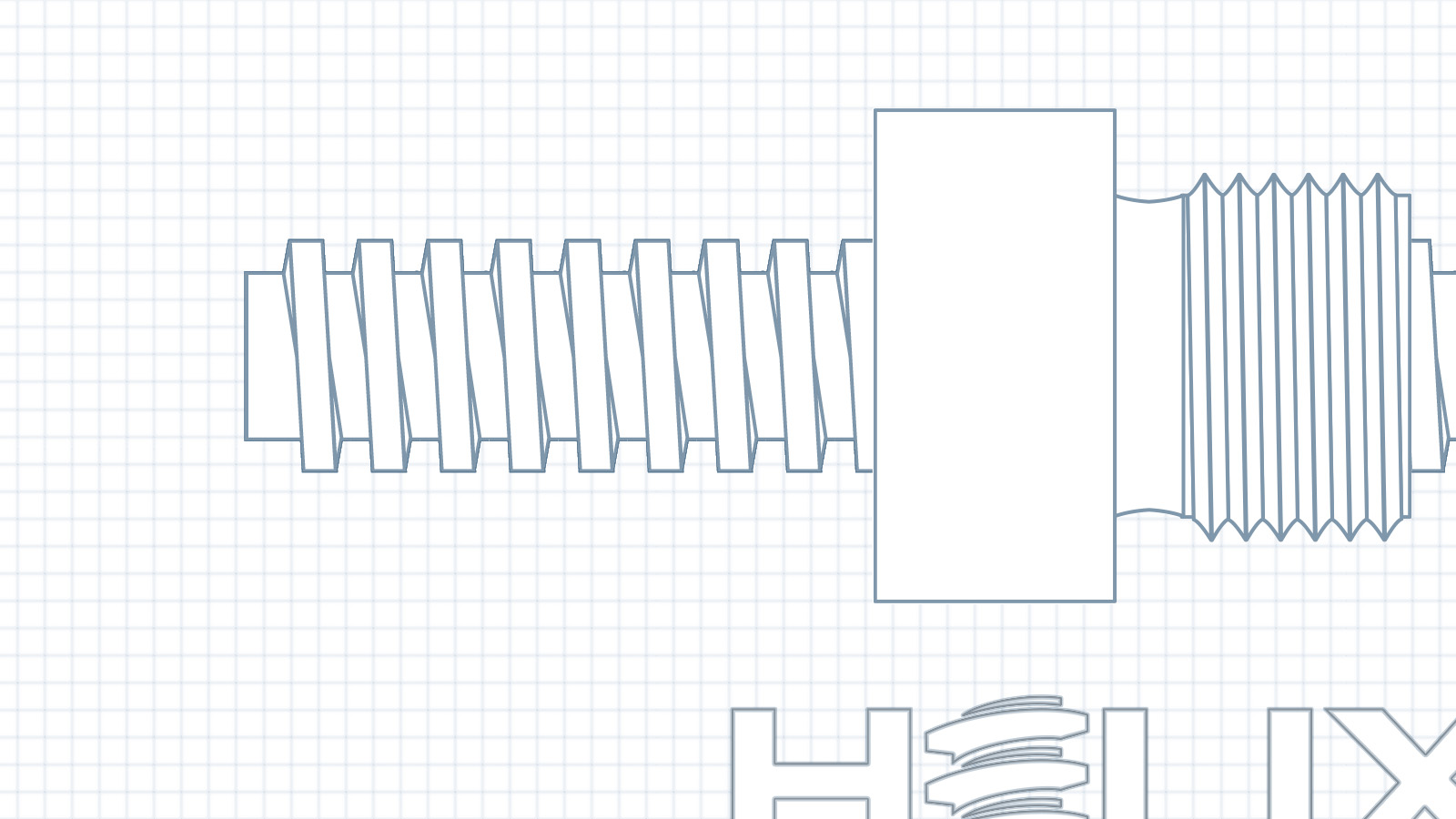
When it comes to linear motion systems, acme screws are a popular choice due to their efficiency, precision, and cost-effectiveness. However, there are several misconceptions surrounding acme lead screws that can lead to less than optimal performance if not properly understood. As an engineer with years of experience in designing and implementing linear motion systems, I'm here to shed light on these misconceptions and provide insights on how to apply acme lead screws effectively. In this blog post, we'll explore common acme lead screw misconceptions and delve into the formulas tools and considerations needed for their successful application.
Misconception 1: All Threads Are the Same
One of the most prevalent misconceptions about acme lead screws is that all threads are created equal. In reality, various thread profiles are available, each with its own advantages and disadvantages. Acme and trapezoidal threads are the most common thread profiles used in linear motion applications.
Acme threads- Profile: A square or trapezoidal thread with a 29° angle.
- Advantages: High efficiency, low friction, good load-carrying capacity.
- Application: Precise linear motion where efficiency is crucial.
- Profile: Similar to acme threads but with a 30° angle.
- Advantages: Cost-effective, suitable for general-purpose applications.
- Application: Less demanding linear motion tasks.
Choosing the right thread profile depends on the specific requirements of your linear motion application. Consider factors like load, speed, precision, and budget when making this crucial decision.
Misconception 2: Lead Screw Efficiency Is Always 90%
Another common misconception is that acme lead screws consistently have an efficiency of 90%. While 90% is a reasonable approximation for many scenarios, it's essential to calculate the actual efficiency for your specific application to ensure accurate performance predictions.
Several factors, including the thread profile, lubrication, material, and preload influence the efficiency of an acme lead screw. To calculate efficiency, you can use the following formula:
Efficiency (%) = (valuable work output/input energy) × 100
Where:- Useful work output is the linear motion produced by the lead screw.
- Input energy is the energy applied to the lead screw.
For an acme lead screw, the efficiency can be expressed as:
Efficiency (%) = (π * μ * tan(λ) / 2) × 100
Where:- μ represents the coefficient of friction between the nut and screw.
- λ is the thread angle (29° for acme threads).
To improve efficiency, choose high-quality materials, use proper lubrication, and maintain the lead screw regularly. Additionally, applying an appropriate preload can reduce backlash and enhance efficiency further.
Misconception 3: Backlash Is Insignificant
Backlash is the play or clearance between the screw and nut in a lead screw system. Many believe that backlash is a minor concern, but it can significantly impact the accuracy and repeatability of linear motion systems.
The formula for backlash in a lead screw system is:
Backlash = [(N - n) / N] × P
Where:- N is the number of threads per inch (TPI) on the screw.
- n is the number of threads engaged between the screw and nut.
- P is the pitch of the screw.
To minimize backlash, consider the following strategies:
- Use anti-backlash nuts: These nuts are designed to reduce the clearance between the screw and nut, improving precision.
- Preloading: Applying a controlled axial force to the nut can eliminate backlash and enhance system accuracy.
- Selecting high-precision components: Choose screws and nuts manufactured to tight tolerances for reduced backlash.
Misconception 4: Lead Screw Nut Materials Don't Matter
The material used for the lead screw nut is often overlooked, but it plays a crucial role in the overall performance of the system. Choosing suitable material is essential to ensure long-lasting and reliable linear motion.
Common materials for lead screw nuts include bronze, plastic, and PTFE (Teflon). The choice of material affects factors such as wear resistance, friction, and load-carrying capacity.
Bronze nuts offer excellent wear resistance but can be noisy and require lubrication. Plastic nuts are quieter and self-lubricating but may not handle heavy loads. PTFE nuts combine low friction with self-lubrication and are suitable for high-precision applications.
The choice of material should align with your specific application requirements. Ensure that the nut material complements the lead screw material to minimize wear and extend the system's lifespan.
Misconception 5: Speed Has No Impact on Performance
The linear speed at which an acme lead screw operates can significantly impact its performance. The relationship between speed, lead, and critical speed must be considered to avoid vibrations and resonances.
The formula for critical speed in a lead screw system is:
Critical Speed (RPM) = (π * √(E / (4 * ρ))) / (2 * L)
Where:- E is the modulus of elasticity of the screw material.
- ρ is the density of the screw material.
- L is the unsupported length of the screw.
Operating the lead screw at or near its critical speed can result in vibrations and reduced precision. To avoid this, stay within recommended operating speeds and consider shorter screw lengths, thicker diameters, or different materials if necessary.
Conclusion
Acme lead screws are versatile components for achieving precise linear motion in various applications. However, understanding and dispelling common misconceptions is crucial to their successful implementation. Engineers can design and optimize linear motion systems that meet their specific requirements by recognizing the importance of thread profiles, efficiency calculations, backlash reduction, nut material selection, and speed limitations.
Remember that each linear motion application is unique, and carefully considering these factors is essential for achieving the desired performance and accuracy. Always consult with experienced engineers and utilize the appropriate formulas to make informed decisions when designing and applying acme lead screw systems. With the proper knowledge and attention to detail, you can harness the full potential of acme lead screws in your projects.