How Lead Screws Effectively Drive Linear Motion In Industrial Robots
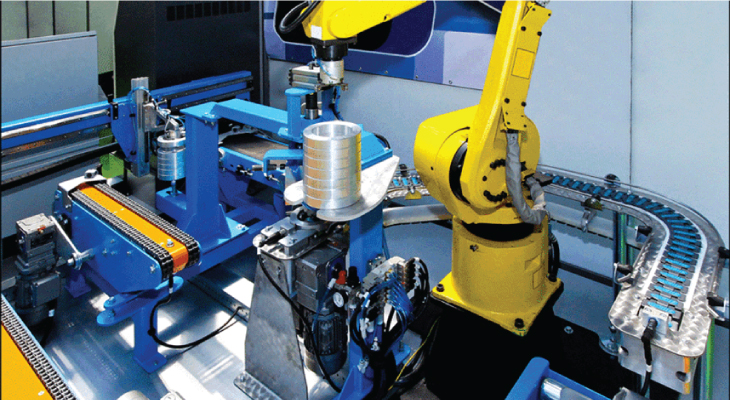
While industrial robots have been used to manipulate parts, tools, materials, and specialized devices for half a century, industrial robot manufacturers face a range of new challenges associated with increased demand for greater levels of adaptability, agility, and flexibility. Challenges that require enhanced linear motion control can be met by a new generation of precision-engineered lead screws.
An industrial robot is a multi-functional mechanical device that can carry out variable motions to manipulate objects and perform specific tasks. Industrial robots are used in various industries, often to grasp, move, and position work pieces for manufacture or assembly. Increasingly, manufacturing companies seek robotic systems that can manipulate objects, pieces, or tools with programmable movements in several degrees of freedom.
Resolving Industrial Robotics Challenges
One challenge facing industrial robot manufacturers is to find ways to position and control robotic movement despite limitations in acceleration and deceleration. Robotic guidance systems typically must combine accuracy, rigidity, and speed. In many applications, achieving high levels of accuracy in stroke movement and rotation on the Z-axis is critical, particularly when high speed and low runout are required. Another limiting factor is weight, especially in applications in which inertia has to be minimized.
A new generation of the precision-engineered lead screw is enabling industrial robot manufacturers to resolve these challenges. Typically, these screws are used to drive changes in the vertical and horizontal orientation of robot arms. This type of screw is used to transform the rotary output from an electric motor into the linear motion needed to drive the joint of the arm. Some screw manufacturers offer optimized thread forms, which can significantly improve performance when combined with lead screw nuts made of specialized materials.
Lead screws offer advantages when compared to other linear motion control mechanisms. These include:
- They cost less
- They are self-locking and do not require a braking system
- They are better for vertical applications
The Helix Linear Technologies Advantage in Industrial Robotics
Precision-engineered screws provide essential advantages for industrial robotic applications. Helix is at the forefront of producing a new generation of precision lead screws that dramatically increases accuracy. Using advanced thread-rolling processes and materials composition technologies, precision-engineered lead and acme screws provide a cost-effective solution for overcoming the linear motion challenges related to industrial robotic systems.
Utilizing the helix angle of the screw thread to convert rotary motion into linear motion and relying on the coefficient of friction between the lead screw nut and lead screw— these lead screws are a reliable mechanism to position loads. Screws are available in various materials, such as carbon steel and stainless steel, and can be paired with an internally lubricated plastic or a bearing-grade bronze nut.
Helix precision lead screw assemblies are compact and incorporate the wear-compensating, anti-backlash design necessary for achieving the precision placement required by industrial robots. The Helix anti-backlash nut design provides excellent lubrication characteristics with the dimensional stability of the firm’s proprietary engineered acetal material. These lead nuts also have the added convenience of an integral flange.
Solving Industrial Robotics Linear Motion Challenges with Lead Screws
Precision-engineered screws can help you resolve your industrial robot challenges. Helix supplies a complete line of precision lead and acme screws and assemblies with thread forms that can optimize the best possible repeatable performance. With Helix precision screws, you will realize greater adaptability, increased agility, and improved flexibility to help meet the increasing demands of industrial robotic systems.