Find the Air in Your Ways - Go Electric
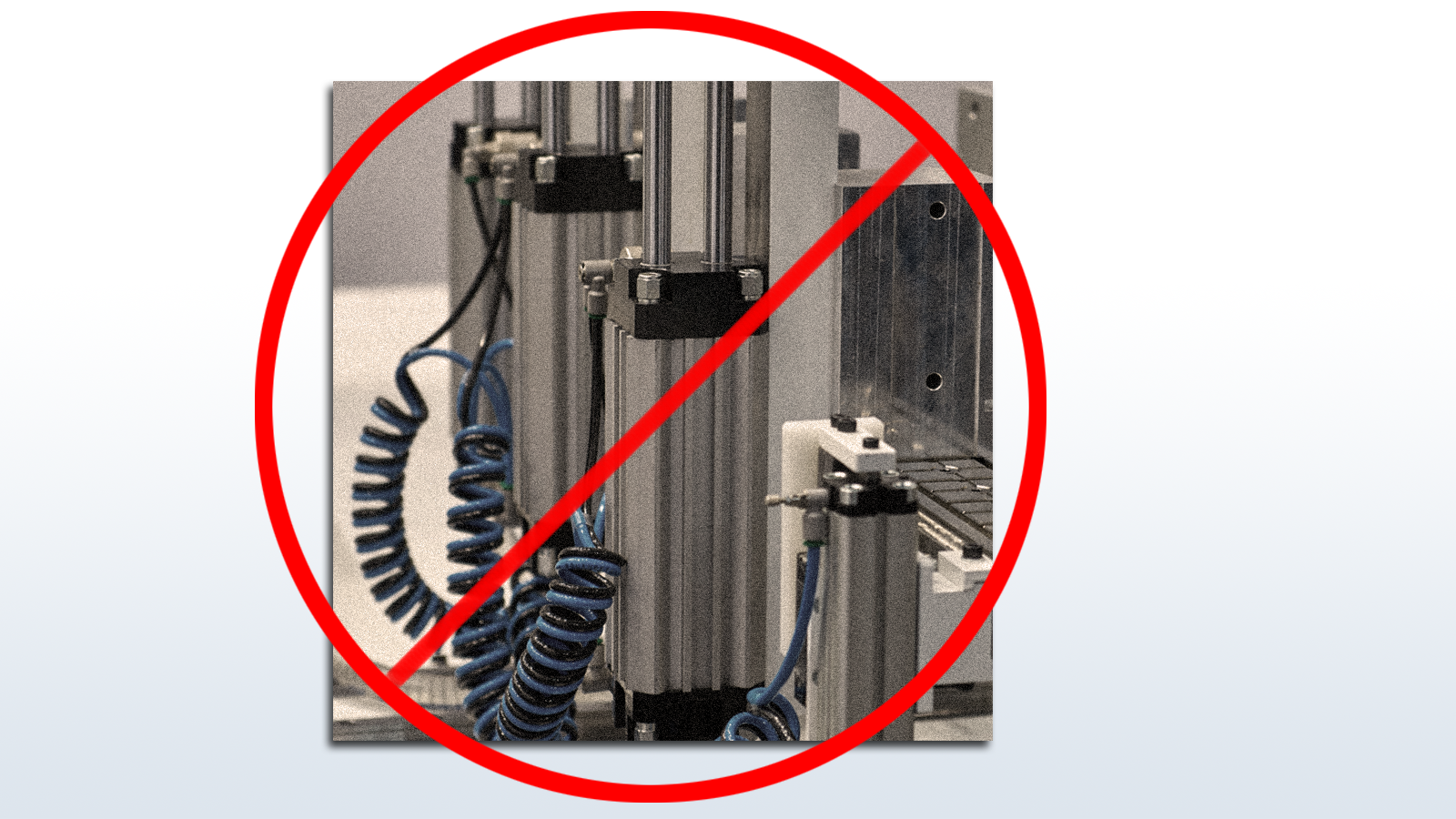
Getting some fresh air is always a good idea, right? It wakes you up, refreshes you, or even changes your mindset. But what happens when the air starts to get stale?
Pneumatic actuators have been the staple of the industry for years and have been sold as being compact, fast, and low cost. Their compact size is due to the remote location of their power unit. The rapid response is due to the sudden inrush of air for activation. Also, the actuator has a low cost because the air cylinder by itself is inexpensive. Electric actuators, like Electric Cylinders, have made steady inroads into the air actuator market due to advances in control technologies, materials and automation disciplines.
But do air cylinders have really low costs? Or is their low cost an illusion? Design engineers sometimes look at them individually, not the sum of the system’s costs, and ignore the costs of providing air. For example, to control the cylinder, you need an electrically operated solenoid valve, regulator, airlines, flow control valves, and a reliable source of clean, dry air. If the cylinder needs to be moved in both directions, which is the requirement in most cases, a dual-stage cylinder and solenoid valve is required, increasing the costs and plumbing complexity.
Most automotive plants are switching to electric cylinders to eliminate an estimated 3% of their plant operating costs of providing air. Electric actuators only require a power source that is readily available and only needed when the actuation is in process. Air compressors run full time-wasting vast amounts of energy, creating heat and noise. It is estimated that electric actuators have an 80% advantage over air cylinders in energy efficiency. The air source must be chilled, dried, oiled, and filtered,d which is 24% of the compressor energy costs. The maintenance cost of this equipment is staggering and the always present leaks in the system, further raising the cost curve. Air actuators are also very noisy in their operation, and their oiled air is released into the environment.
Electric actuators require control to move them. The costs will be prohibitive if we put in a move profile, which is challenging with air actuation. With the advancements in control technology, stepper motor drivers can easily interface to the machine via can bus at the exact price as a dual solenoid control valve mounted to a manifold. Helix offers a simple lead screw stepper-driven actuator for under $80, and control can be purchased for $90 to $230, depending on the application.
Unlike their air counterparts, electric actuators can stop mid-cycle, have a programmable move profile, handle higher loads, move more smoothly, and provide variable speed and stroke. They also require no hard stops, provide high levels of precision motion and only use power during actuation. Because air is compressible, it is impossible to achieve a uniform and constant piston speeds, and air cylinders may move after being positioned because of the compression causing other system issues. Manual setup of the airflow control valves for air cylinders is tricky, and odds are they will need adjusting regularly. Electric actuators are cleaner, as they do not have the oiled air mist discharged from the air cylinders.
If your process requires routine changeover, electrical actuation is the way to go. It becomes a programming issue that can be easily downloaded to the family of actuators rather than manually adjusting many air cylinders. Electrical actuators don’t require full retraction, which may reduce cycle times. Electrical actuators also can be integrated into touch controls to maintain a certain pressure, which is very popular in welding applications.