Lead Screw Automation Flexibility Key to Medical Device Manufacturing
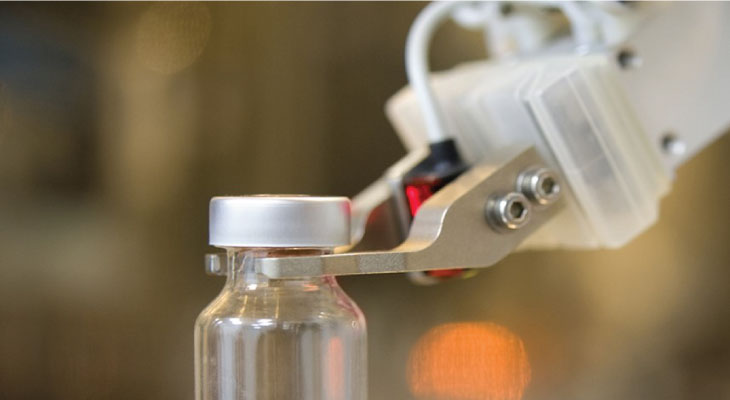
The only constant is change, especially for medical device manufacturers, who face ongoing pressures to introduce new products or highly modified versions of existing devices faster than any other industry.
While precision automation is a proven strategy for helping medical device manufacturers respond to industry demands for innovation and accelerate time-to-market, not just any automated system will do. Medical manufacturers require flexible, modular linear motion control and automation systems to sustain the agility necessary to respond to the rapid pace of new product development while complying with stringent regulatory requirements. Lead screws and stepper motor actuators are excellent solutions for medical device applications because they are precise, clean, and quiet.
Why Flexibility is Critical
When you're assembling different medical device designs or device models within the same facility, moving products efficiently and cost-effectively is paramount. By using a modular, automated transport system that utilizes lead-screw-based linear actuators, medical manufacturers can reap the time and cost benefits of having flexible options for routing, positioning, orienting, conveying, and stopping products.
With a modular motion control system, you will enjoy layout flexibility, enabling you to incorporate 90-degree movements, numerous types of curved motions, and vertical lifts into your conveyor transport system. This will allow you to maximize the use of your facility footprint and available space and identify less costly ways to re-route or re-orient products.
Modular linear actuators also provide precision positioning options for robotic or automated applications, vital for medical manufacturing. Tasks such as gluing, soldering, welding, or picking and placing objects may require extreme to varying degrees of precision. With modular positioning units that use lead screws, you can realize up to .0003"/inch (higher accuracy upon request) positioning accuracy for facilitating either manual or automated assembly.
In short, flexible, modular motion control systems are critical for medical device manufacturing because of the many line changes, reconfigurations, and repositionings required to handle various types of products. With a modular lead-screw-based linear motion control system, you will enjoy mounting simplicity, accurate repositioning, and optimized workflows in both manual and automated assembly processes.
The Advantages of Modular Automation Systems
Although fully automated production systems generally are more thought of in connection with products with long life cycles or high-volume production runs, the investment makes obvious operational sense. They also carry advantages for manufacturing and assembling medical devices with short life cycles or low-volume production runs when designed modularly. These systems can enable medical manufacturers to leverage sophisticated equipment and/or unique human talents repeatedly.
Many medical manufacturers overlook the benefits of automated production because they think automation refers to packaging when, in fact, it makes the most sense in the medical device industry. Because medical device manufacturers are highly regulated, they focus on the principle of Total Quality Management (TQM) as a necessary quality management model for complying with governmental regulations. Of course, a fully automated production system that uses lead-screw-based motion control systems throughout the entire product planning and product lifecycle is the best way to meet TQM requirements.
Medical manufacturers can dramatically reduce cost per unit produced, improve quality, and maximize resource utilization by configuring modular conveyors, Cartesian robots, motion control systems, and automated tools for assembly, testing, and packaging medical devices. Other advantages of modular automation systems for medical devices include:
- Elimination of errors, corrections, and rework
- Optimization of inventory and resource utilization
- Reductions in production delays
- Waste minimization
- Better use of human resources adds value
Important Variables to Consider
When considering whether to implement full production automation that relies on motion control systems, it's prudent to view all the variables that come into play:
- Do you have enough volume—in terms of either single-product quantities or multiple products—to support it?
- Are your product life cycles short or long? Do you have time to reconfigure between product runs?
- Can the system handle delicate and sensitive components and materials, an essential requirement for medical products?
- Is the system compatible with a clean room environment?
- Can the system support a range of automated processes, such as inspection and testing?
- Does the system provide the repeatability and reliability that you need?
- Will the system accelerate throughput and reduce costs?
Driving Medical Manufacturing Automation with Linear Motion Control
By implementing flexible, modular linear motion control and automation systems, medical device manufacturers can overcome the pressures of introducing new products or highly modified versions of existing devices at a frenzied pace. These systems can allow you to efficiently and cost-effectively respond to the rapid pace of new product development while complying with stringent regulatory requirements.
To learn more about lead-screw-based linear motion control systems that can help you drive flexible, modular automated medical devices, download a copy of our syringe pump case study here.