Lead Screws: How Small Size Doubles Duty in Medical Device Design!
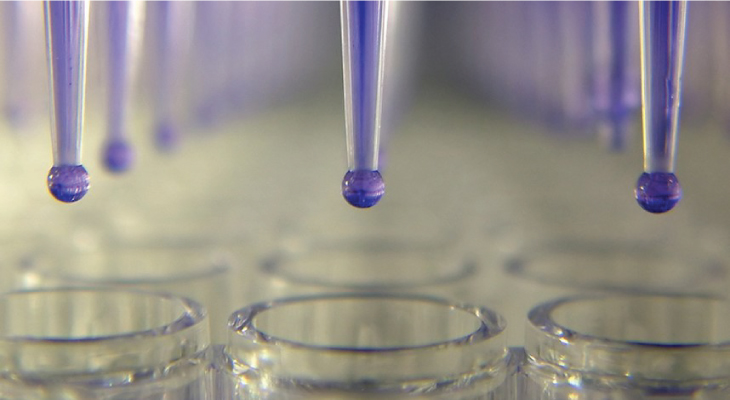
Acme lead screws small size doubles duty
Helix has recently introduced its precision miniature lead screw designs for light load medical device design and applications that deliver fast speed and close tolerance positioning. Designed for compact applications that require the dual ability to be fast and precise - ideal for accurate positioning requiring a rapid approach and retraction.
Helix engineers use their expertise in designing for a vast array of different industries and their unique applications within each. One industry, in particular, is the medical and diagnostics industry, where an acme screw is an answer to the linear motion needed in a lot of medical applications.
However, the combination of small screws and high - precision is also well suited for a myriad of broad-based light load applications requiring close positioning and fast speed, including; military, optics, instrumentation, sensors, etc.
Advanced medical device designs are evolving rapidly and demand higher standards for medical equipment reliability. Applying linear motion components to these medical applications yields the best results when collaboration begins at the early stages of the design. Modification to current parts or a custom design may offer the optimum solution; therefore, teamwork must be emphasized with medical device manufacturers during the early stages of design.
Medical application specifications often exceed the capabilities of standard, cataloged products. Helix leverages its decades of expertise when modifying standard parts or creating custom designs for medical applications—at the same time, utilizing robust quality systems, a vertically integrated manufacturing model, and implementing a disciplined product realization process.
According to Helix CEO Christopher Nook, "We often start with the customer's performance specifications focused on the product's expected life, environmental conditions, material selection, and physical size. We then incorporate enhancements to the product's design that address the rigors of most medical applications. This process has allowed us to sell modified standard products to the medical industry successfully."
Medical Device Design Priorities
Beginning with specification requirements provided by the medical device manufacturer, a definition of design priorities must be incorporated for finished devices intended for human use, including:
- Performance: load capacity and length/range of travel requirements
- Efficiency: high-precision/low-precision
- Envelope: compact
- Material Constraints: stainless steel, magnetism/non-magnetism, radioactive elements, etc.
- Operating Environment: non-direct exposure with patients or attached to the human body, etc.
Medical Device Design Reviews
Design reviews are conducted at various stages involving comprehensive, systematic, and documented examinations of a design that will evaluate the design requirements' adequacy and evaluate the design's capability to meet these requirements.
Designing a small diameter lead screw is not practical if it can't be consistently and efficiently produced. Helix leverages SolidWorks© COSMOS software at this stage to provide a full range of integrated modeling and simulation that medical product manufacturers need to design better products faster - and at a lower cost.
Medical Device Design Trends/Products
- Small diameter lead screw for compact/precision applications
The growing worldwide shift toward smaller packaged applications typically requires lower load capacity and higher precision. Small diameter screws are designed for smaller footprint applications to meet the needs of these medical applications. In addition to medical equipment, these screws are used in robots, guided missiles, unmanned vehicles, and aerospace applications.