Advantages Linear Motion Suppliers Have in Medical Industry
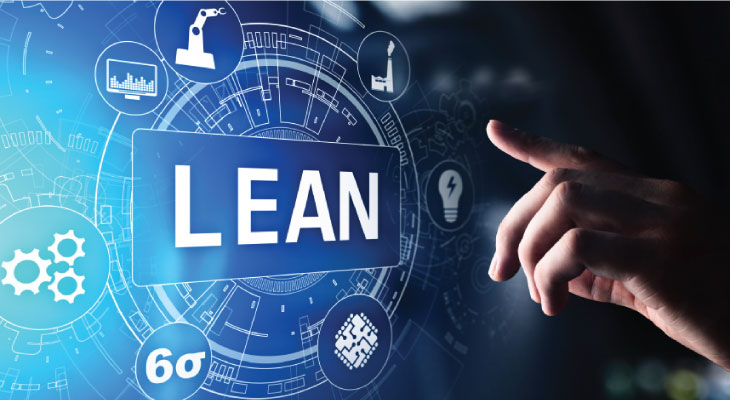
Companies spend millions of dollars each year on improving productivity through Lean initiatives. Kaizen events use Value Stream Mapping and SMED tools to eliminate non-valued added work, reduce cycle times, increase throughput, and improve changeover time. Unfortunately, many of these efforts are not initiated until after a product has been designed and released. Design for Manufacturing (DFM) addresses many issues upfront -- driving down manufacturing costs and eliminating waste.
Rather than asking, "what's the cost of doing something," ask, "what's the cost of not doing it," to help put the decision-making process into perspective.
The average development time for a medical device/lab equipment is three to seven years, with a research and development price tag exceeding $2,000,000. Once brought to market, these machines generally provide eight to ten years of service life. The cost of downtime for these users, especially unplanned, is exceptionally high. A field service call can reach $15,000 per incident depending on the problem, location of the device, and the specialized service personnel required to fix it. Costs of this magnitude can easily erase any savings realized in manufacturing. Added to this cost is the potential loss of revenue from the sale of consumables, loss of business due to quality issues and company reputation, and, most critical -- malfunction complications during patient care.
The cost per square foot of floor space (both for the OEM's shop and the end-user like a doctor's office, lab, or hospital) is constantly increasing. In addition, as the industry evolves, smaller point-of-care equipment demand continues to rise, necessitating the manufacture of devices with smaller footprints. For example, years ago, it was uncommon for medical applications to require lead screws or ball screws under 8 mm in diameter. Now, numerous applications use ball screws as small as 4 mm and producing lead screws with 2 mm diameters is a daily occurrence in our facility.
However, smaller footprints do not always have to come at the expense of throughput. For example, improving throughput provides additional capacity, reducing the number of machines necessary to meet production volume. Or it can allow more machines to be placed in the same area, resulting in increased revenue per square foot of manufacturing space.
When you partner with a precision linear motion provider like Helix Linear Technologies you will receive the best product we have to offer to fit the needs of your medical application.
Contact one of our application engineers today to get started on your next linear motion project.