Rolled vs. Ground Ball Screws: Understanding the Differences
Ball Screw Manufacturing and Precision Differences
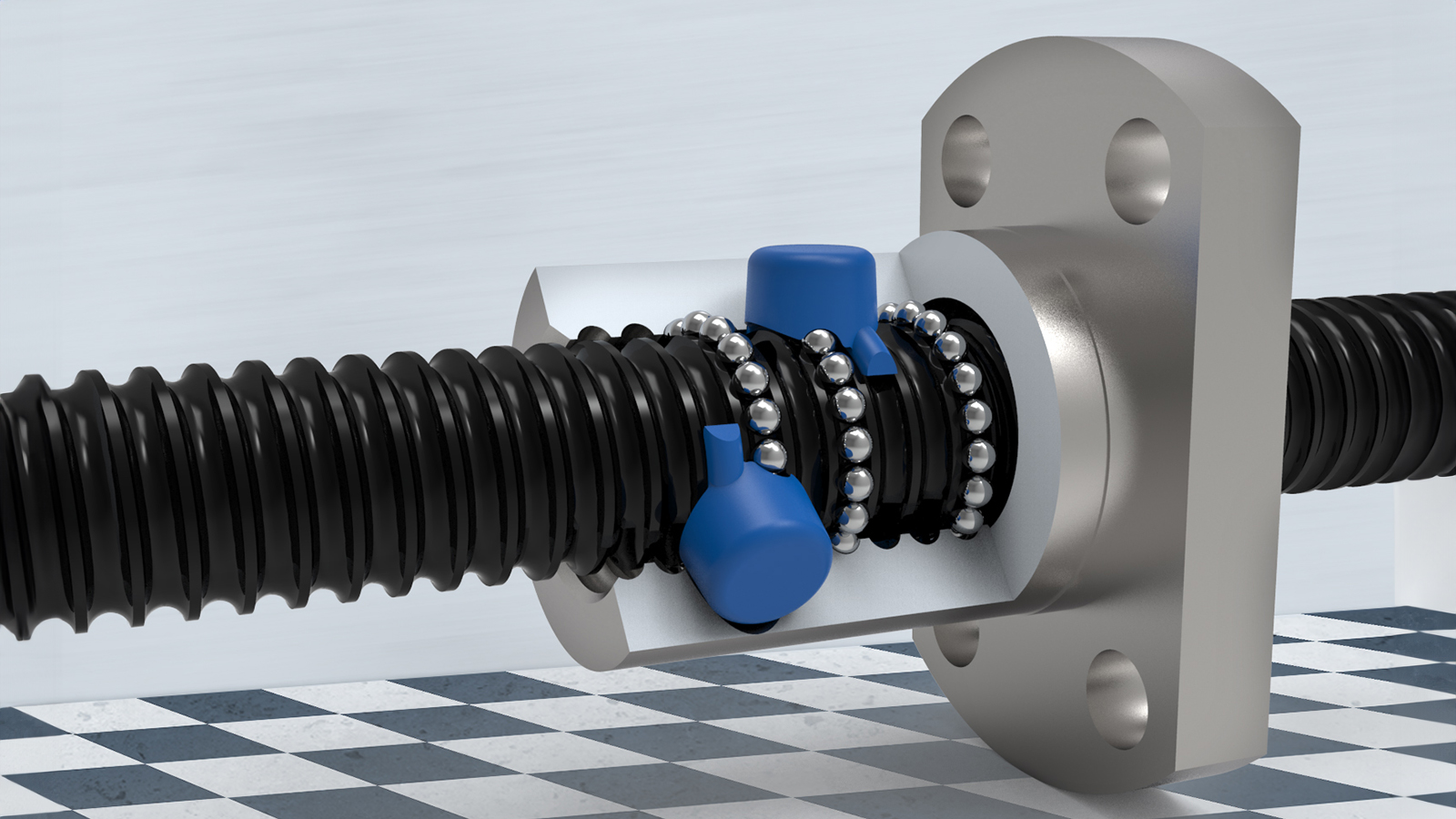
When it comes to selecting the right ball screw for your application, you'll likely encounter two main types: rolled and ground screws. While both serve the same fundamental purpose – converting rotary motion into linear motion – there are key differences in their manufacturing processes, accuracy, cost, and overall suitability for specific applications. In this blog post, we'll be comparing rolled versus ground ball screws so that you can make an informed decision.
Manufacturing process
The manufacturing processes for rolled and ground ball screws are fundamentally different, affecting their performance and application suitability.
Rolled ball screws
Rolled ball screws are produced by pushing a round blank bar material through rotating tool dies. This method uses a cold work deformation process, shaping the threads without removing any material. The efficiency of this process is a considerable advantage, as it allows for high production rates and easy automation.
Ground ball screws
In contrast, ground ball screws undergo an abrasive machining process. The blank bar is rotated between two machining centers, where hard abrasive cutters carve out the threads. This method is more time-consuming and typically requires that the material blanks be cut to length before grinding, making ground ball screws more of a customized product.
Custom Ball Screws
Many applications require a custom design of a ball screw. The simplest of modifications requires the ends of the ball screw to be modified to accommodate a bearing support. More demanding designs require a custom ball nut that meets higher static and dynamic load requirements. Customizing a ball screw can get complicated and partnering with a company that has all of the manufacturing capability to manufacture the entire assembly can shorten the lead time and keep costs at a reasonable level.
Accuracy
Accuracy is another crucial difference between rolled and ground ball screws.
Rolled ball screws
Rolled ball screws can provide acceptable precision, sometimes reaching tolerances of around 23 microns. However, they typically fall short compared to their ground counterparts. Rolled screws tend to have rougher surface finishes, which can lead to increased friction and reduced mechanical efficiency.
Ground ball screws
Ground ball screws excel in accuracy, with capabilities of achieving tolerances as tight as 3 microns. This level of precision is particularly imperative in applications where repeatability and positional accuracy are essential. The grinding process also allows for better concentricity between the screw and the bearing surfaces, resulting in smoother operation.
Cost
Cost is a significant factor to consider when choosing between rolled and ground ball screws. Many times a custom ball screw is required for an application.
Rolled Ball Screws
Due to their efficient manufacturing process, rolled ball screws are generally much less expensive than ground ball screws, sometimes costing over 50% less. This affordability, combined with faster delivery times, makes rolled ball screws an attractive option for many applications that do not require high precision.
Ground Ball Screws
While ground ball screws carry a higher price tag due to their intricate manufacturing process, their superior accuracy often justifies the cost in applications that demand high precision and repeatability.
Strengths and limitations
Both rolled and ground ball screws come with their strengths and limitations. Rolled ball screws offer a cost-effective and efficient manufacturing process, making them suitable for many applications where precision requirements are not as stringent. They provide sufficient accuracy for most uses but are more susceptible to dimensional distortions over time due to tooling wear. Additionally, the rougher surface finish of rolled ball screws can increase friction and reduce wear resistance.
On the other hand, ground ball screws provide superior accuracy and repeatability thanks to their finer surface finishes, which also contribute to quieter operation and reduced friction. However, these benefits come at a higher cost, with longer lead times and a more time-intensive manufacturing process.
Which should you choose?
The choice between rolled and ground ball screws ultimately depends on your specific application needs. Should you need a totally custom ball screw design, we can certainly help with the sizing, design and manufacture.
Here are two tips to help you choose:
- Rolled ball screws – Choose rolled ball screws if your project requires a cost-effective solution where high precision is not critical. Rolled ball screws are appropriate for a wide range of applications and provide excellent value.
- Ground ball screws – Choose ground ball screws if your application demands extremely high precision and repeatability. They are suitable for high-performance machinery where accuracy is essential.
Conclusion
Both rolled, and ground ball screws have their distinct advantages and are available in various sizes and capacities to suit a wide array of applications. By understanding the differences in manufacturing processes, accuracy, cost, and overall strengths, you can make a more informed decision about which type of ball screw will best meet your project's needs. Whether you choose the affordable rolled ball screw or the highly accurate ground ball screw, there's an option that will work well for your needs.