Selecting the Best Drive for a Stepper Motor Linear Actuator
A Comprehensive Guide for Mechanical Engineers
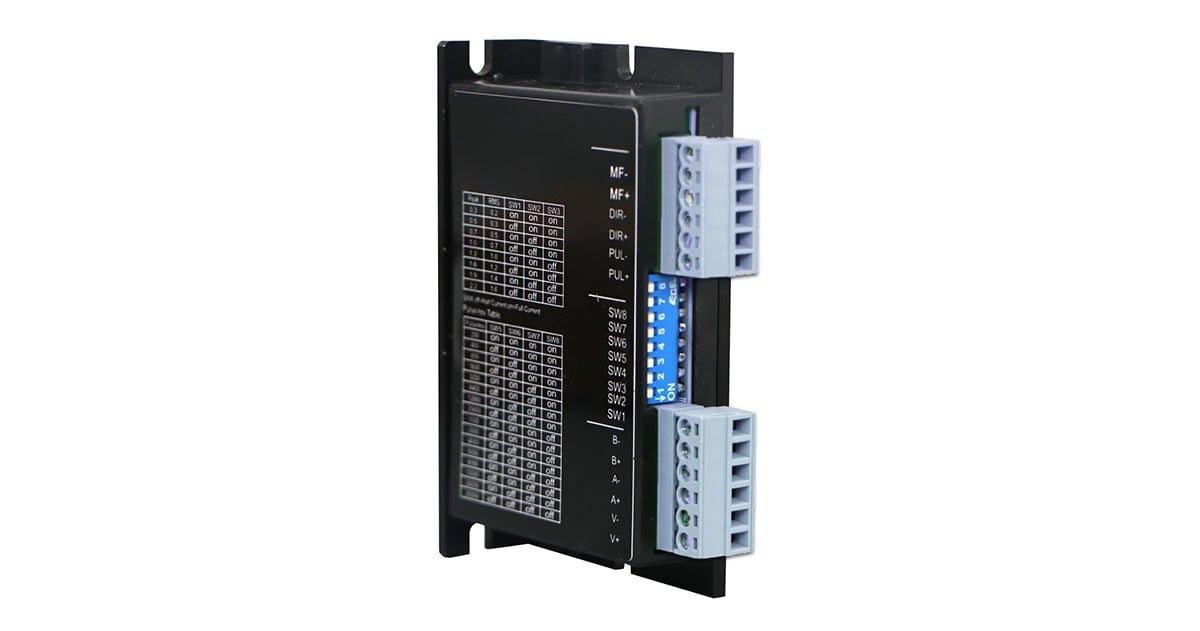
Discover the key factors to consider when selecting a drive for your stepper motor linear actuator. Dive into the world of mechanical engineering as we explore the various options, benefits, and challenges associated with choosing the ideal drive for your application.
Introduction
As a mechanical engineer, you understand the critical role that a stepper motor linear actuator plays in various industrial and automation applications. The stepper actuator is a versatile device known for its precise positioning capabilities, making it an excellent choice for applications that require accuracy and control. However, to ensure optimal performance and functionality, selecting the best drive for your stepper motor linear actuator is crucial. In this comprehensive guide, we will explore the key factors to consider when choosing a drive, the available options, and address frequently asked questions on the topic.
What are the Different Types of Stepper Motor Drives?
When selecting the best drive for your stepper motor linear actuator, it's essential to understand the different types available. Let's explore two common types:
Pulse-Driven Drives: Pulse-driven drives, also known as open-loop drives, are a popular choice for many stepper motor applications. These drives operate by providing discrete pulses to the stepper motor, causing it to move in precise increments. The simplicity and cost-effectiveness of pulse-driven drives make them suitable for applications where high precision isn't the primary concern.
Feedback-Controlled Drives: Feedback-controlled drives, or closed-loop drives, are designed to address the limitations of open-loop drives. They utilize encoder feedback to ensure accurate positioning and overcome issues like missed steps or motor stall. Feedback-controlled drives are ideal for applications that require higher precision, such as robotics, CNC machines, or 3D printers.
What Factors Should You Consider When Selecting a Drive?
Choosing the best drive for your stepper motor linear actuator requires careful consideration of several factors. Let's delve into the key aspects to keep in mind:
Precision Requirements: Determine the level of precision your application demands. For tasks that require high accuracy, a feedback-controlled drive may be necessary, whereas pulse-driven drives may suffice for less demanding applications.
Load and Torque: Analyze the load and torque requirements of your application. Different drives have varying torque capabilities, and selecting a drive that can handle your desired load is essential for optimal performance and longevity.
Speed and Acceleration: Consider the desired speed and acceleration profiles of your application. Some drives may have limitations in terms of maximum speed or acceleration, which can impact the overall efficiency and productivity of your system.
Environmental Conditions: Evaluate the environmental conditions your stepper motor linear actuator will operate in. Factors such as temperature, humidity, dust, and vibration levels can influence the choice of drive, as certain drives may be better suited to withstand harsh conditions.
Cost Considerations: Budgetary constraints often play a significant role in the selection process. Assess the cost-effectiveness of different drive options while keeping in mind the required functionality and performance.
Which Drive Control Method Should You Choose?
The control method employed by the drive can significantly impact the operation and capabilities of your stepper motor linear actuator. Here are two common control methods to consider:
Full-Step Control: Full-step control is the simplest control method, where the stepper motor moves in full steps. While this method provides a higher holding torque, it may lack precision compared to other control methods.
Microstepping Control: Microstepping control divides each full step into smaller microsteps, allowing for smoother motion and increased positioning accuracy. However, it may come at the expense of reduced torque, so consider the trade-offs between precision and torque when choosing this control method.
Frequently Asked Questions
Can I use a pulse-driven drive for applications that require high precision?
Pulse-driven drives can provide sufficient accuracy for many applications. However, for tasks demanding extremely high precision or those susceptible to missed steps, a feedback-controlled drive is recommended.
How can I ensure my stepper motor linear actuator operates reliably in harsh environments?
To enhance the durability of your stepper motor linear actuator in challenging conditions, consider choosing a drive specifically designed for rugged environments. Look for drives with protective features such as sealed enclosures, enhanced temperature resistance, and robust construction.
What are the advantages of using a feedback-controlled drive?
Feedback-controlled drives offer improved accuracy and reliability by continuously monitoring the motor's position. These drives can detect errors, correct missed steps, and provide real-time feedback, making them ideal for applications where precision is critical.
Conclusion
Selecting the best drive for your stepper motor linear actuator is a crucial decision that directly impacts the performance and functionality of your application. Considerations such as precision requirements, load and torque, speed and acceleration, environmental conditions, and cost considerations, you can make an informed choice. Whether you opt for a pulse-driven drive or a feedback-controlled drive, understanding the various options and their benefits will help you achieve the desired results. Remember to analyze your specific application needs and consult with experts when necessary to ensure the best drive selection for your stepper motor linear actuator.