The Importance of Proper Lubrication for Acme Screws
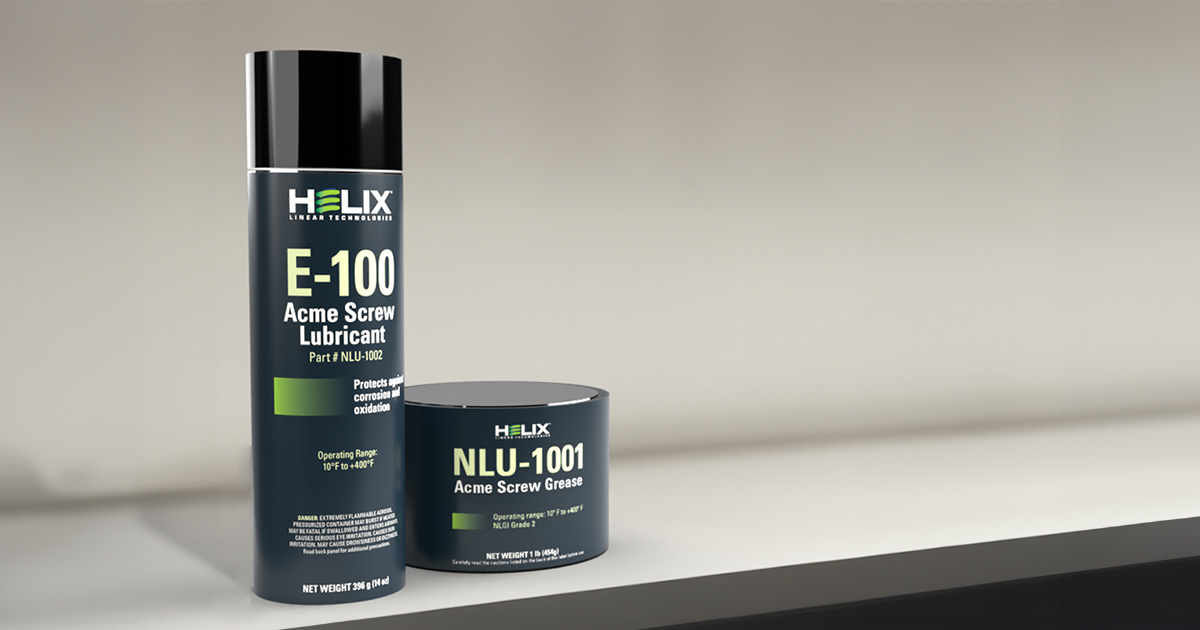
Prolong acme screw assembly reliability and life
The coefficient of friction, wear life, and resulting torque to drive lead screws and acme screw assemblies are highly controlled by the ability of the engineered plastic to supply sufficient lubrication to the nut and screw interface.
Many factors have to be considered when designing and selecting a precision acme screw. Environment, operating load, accuracy, and speed are important factors to consider in the design decision. Unlike ball screws, acme lead screws with bronze or polymer acme nuts tend to have higher friction and more wear - making proper lubrication a vital part of the performance and increased life.
Benefits of a proper lubrication
There are several main benefits of using proper lubrication, including:
- Sheer Stability
- High-Temperature Resistant
- Corrosion Protection
- Separation Resistant
- Extreme Pressure Properties
- Shelf Stable
- Water-Resistant
Extend life and longevity
Precision acme screws are manufactured from high-quality materials with excellent dynamic properties. A specific life cannot be predicted because of the variable effects of friction, lubrication, and cleanliness. Proper lubrication, regular maintenance, and operation within specified limits will extend the screw's life and longevity.
The application determines lubrication intervals. It is required that screw assemblies are lubricated often enough to maintain a lubricant film on the screw.
Importance of efficiency
The efficiency of precision acme screw assemblies ranges from 15% to 85%. These efficiencies are dependent upon the nut material, lubrication, lead, and thread form.
Temperature precautions
With proper lubrication, acme screws with bronze nuts operate efficiently between 15°F and 350°F, and plastic nuts between 15°F and 175°F.
Proper lubrication must be provided to achieve a satisfactory service life for your acme screws and acme screw assemblies. It is required that screw assemblies are lubricated often enough to maintain a lubricant film on the screw.
Lack of lubrication
Lack of lubrication can reduce the life and performance of the acme screws and the entire machine. Frequently, a lack of lubrication can cause erratic drag torques and unpredictable wear.
Specifying a lubricant
Even self-lubricated nuts can benefit from using light grease and can also reduce heat in these units.
Excellent and consistent lubrication has long-term benefits and is more critical to an application than whether the screw was cut or rolled. When maximum performance is required in the most demanding applications, using the proper lubricant and the proper amount can help you reach full productivity.
Specific applications require more/less lubrication, external/internal lubrication, and more/less maintenance. When lubricants are applied correctly, they can provide unique capabilities that may be difficult to obtain without using any lubricant.