A Guide to Precision Ball Screw Assemblies
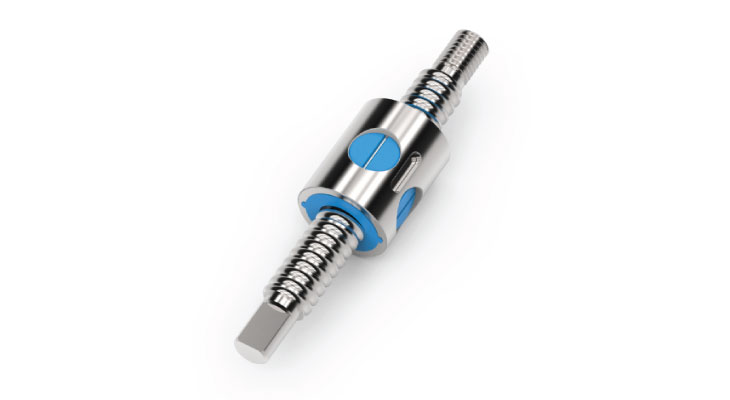
How Are Ball Screws Manufactured?
Ball screws are manufactured by rolling or grinding the threads. In some specific situations, they are whirled due to end machining features or tooling availability. Otherwise, rolling and grinding are the primary and preferred methods of ball screw manufacturing.
Thread rolling is an efficient and economical way to produce precision ball screws. The manufacturing process follows the same principles of lead screw rolling. Heat hardened dies are used to cold form the material without removing metal. The primary difference between ball screws and lead screws is the die design for thread form. Lead screw thread forms are generally acme, stub acme, or trapezoidal variety. However, the ball screw form is a gothic arch shape needed to conform to the balls rolling between the threads.
Ball screws are rolled out of alloy steel or stainless-steel grades that can be hardened by heat treating. The hardened ball screw material must hold up to the hardened balls loaded in the ball screw nut. The hardness prevents excessive wear from occurring and eliminates material fatigue, which can cause catastrophic failure.
One benefit of thread rolling ball screws is manufacturability. Rolled ball screws are generally formed in 12-foot lengths and are then heat-treated in these long lengths before being cut and machined. Due to the through-feed rolling process (where the dies apply pressure from different sides), extremely small diameters can be produced in these long lengths with minimal concern about the length to diameter ratio. On the other hand, grinding a ball screw requires a grinding wheel that will contact the ball screw radially. The side pressure against the shaft can create bending or deflection problems if the length to diameter ratio is too large. A steady rest can be used to support the shaft, minimizing deflection. Still, limitations exist with grinding, including the maximum distance between centers that the machine can handle.
Precision rolled ball screw assemblies can be manufactured with reduced backlash by a selective fit process. Ball sizes are available in 5-micron increments. Appropriate ball size is selected for a ball screw assembly based on the pitch diameters of the ball screw and ball nut. Thus, the same low-lash specs can be achieved with the rolled ball screw.
Ground ball screw assemblies have tighter backlash specs and are used in applications where less axial lash is needed. However, the cost of a ground screw can be considerably higher than a precision rolled ball screw, especially in longer lengths.
Ball Screw Accuracy Grades
The accuracy grades of ball screws commonly fall into six categories, C0, C1, C3, C5, C7, and C10. The lower the number, the higher the precision of the ball screw. The grades are based on criteria related to travel accuracy and variation. Travel accuracy is the linear accuracy tolerance over a specified travel distance. The variation is the allowable variation over a narrower range of 300mm and also the variation in one revolution. Based on the maximum limits of both criteria, grades C0 through C5 are referred to as precision ball screws. Grades C7 and C10 are considered standard ball screws.
Traditionally, C0 through C5 precision ball screws have been synonymous with ground ball screws and C7 through C10 with rolled ball screws. The charts depicting ball screw precision and categorizing them by ground vs. rolled manufacturing methods were established. Rolled screw technology has improved over the last several years. Innovations in CNC thread rollers with chillers and dynamic variation control produce high linear accuracy with low variation that rival their ground screw counterparts. Precision-rolled ball screws can reach accuracy grades as high as C5 or C3 in shorter strokes.
Five Advantages of Ball Screws
1 - High Efficiency
Ball screws provide a higher level of mechanical efficiency, roughly 90%. This high-efficiency percentage allows ball screws to convert about nine-tenths of an application's rotational motion into linear motion.
2 - Load Capabilities
The reason ball screws are widely used in many different industries is their ability to carry extremely heavy static and dynamic loads at fast, efficient speeds. Ball screws can hold heavy loads due to the recirculating steel balls that support the load. The load ratings for Helix Linear Technologies' ball screws are calculated based on the DIN standard.
3 - Low Friction
Ball screws are extremely low friction (.003) and don't generate the heat that can degrade the nut and accelerate wear. Less friction is achieved by linear ball bearings that recirculate within the ball screw nut. The rolling motion of the ball bearings creates a smooth low-friction gliding surface. Since ball screws produce minimal friction, they are highly reliable and offer a longer service life than a lead screw.
4- High Accuracy and Repeatability
Ball screws are also very popular in most industries because of their accuracy. When considering accuracy, the backlash is a significant factor. Backlash is caused by the clearance between a ball bearing element and screw and nut tracts resulting in no motion in the screw. Ball screws are often preloaded to remove backlash.
5 - Ball screw assemblies do not have PV limitations.
With lead screws, consideration must be given to the combination of loads (pressure measured in PSI) and speeds (velocity – measured in surface feet per minute).
Critical Speed Considerations
Many of the factors that impact column bending also assist in determining and improving critical speed. Based on the linear speed required, calculations should ensure that rotation speed does not exceed 80% of the critical speed. Critical speed factors include ball screw diameter, unsupported length, and how the ends are supported. It is recommended to increase the lead to reduce the RPMs. Increasing the ball screw diameter and end support conditions will help.
Ball Screw Nut Design
Standard ball screw nuts (or ball nuts) come with flange, thread, or keyway mounting configurations. The technology that recirculates the balls from one end of the nut to the other varies based on design and manufacturer. The recirculation can occur externally of the nut using ball tube returns or internally using deflector or end caps. Depending on the ball screw lead or pitch, there may be two or more of these recirculating channels inside the nut, called circuits. The type of recirculating design and the number of circuits in a ball screw nut can influence the overall ball nut size, specifically the outer diameter. It can also impact the nut's dynamic and static load rating for the same size ball screw diameter.
Custom ball screw nuts can be designed and manufactured to meet specific application requirements. Features can be added for functionality, adaptive mounting types, and alternative shapes to address space constraints can be challenging with a traditional ball screw nut.
The manufacture of quality ball screw nuts requires precision machining. However, a custom ball nut can be produced on the same machines and, in some cases, may not be more challenging to create. Complexity often occurs in the actual design of the ball nut. Helix Linear Technologies Application Engineers can collaborate with customers in that effort.
Custom ball nut designs are necessary in cases where the ball screw nut is driven and the ball screw is mounted stationary in tension. This technique is used for very long stoke lengths and where the linear speed requirement exceeds the critical speed of the ball screw. The ball screw nut is mounted in a bearing spindle assembly and driven by a gear or belt coming off the motor. Another unique condition requiring a custom design occurs when multiple nuts are mounted on the same ball screw. This arrangement is common in slitting machines for the paper, film, textile, and food processing industries.
Ball screw nuts come with optional brushes or wipers that generally attach to the face of the ball screw nut, inserted in counter bores at each end. These brushes/wipers prevent dust and debris from reaching the inside of the nut, which can impact the balls rolling smoothly. They also assist in the containment of lubricant inside the nut. In addition, felt wipers can support lube for life requirements.
Ball Screw Linear Actuators
Taking ball screw assemblies one step further, linear actuators built with ball screws provide all the benefits of the heavier load carrying capabilities, low friction, higher efficiency, and reduced wear in a packaged assembly. Ball screw actuators from Helix Linear Technologies are available in rod-style electric cylinders and ball screw linear slides and stages. Ball screws can also be integrated directly into stepper motors, creating a motorized ball screw linear actuator with the elimination of a coupling, increasing the stroke length. In addition, the lower drive torque required to drive the ball screw provides additional motor torque to move the application load.
Overall, from our cost-effective cold-forming ball screw thread rolling process to customizable ball screw nuts, ball screw assemblies from Helix Linear Technologies are ideal for your precision linear motion needs. Our ball screw products optimize applications that require movements of heavy loads, high efficiency, and low friction. Contact one of our application engineers for more information or to implement ball screw assemblies in your next project!