Trapezoidal Screws: Four of The Best Critical Design Considerations
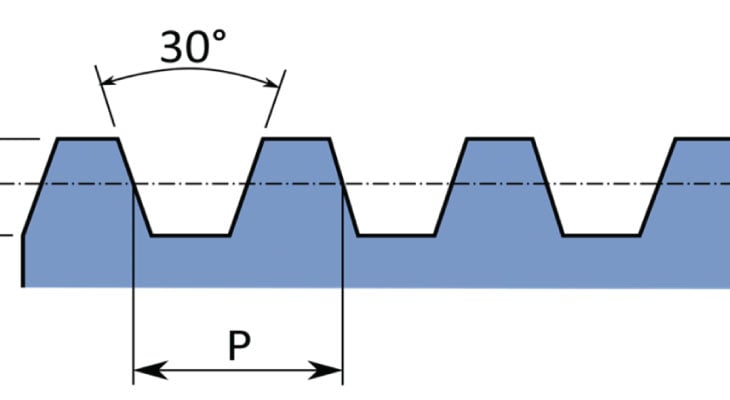
Regardless of the details of any given application, some pretty essential design considerations should be addressed every time you consider trapezoidal screws as a means of linear motion. In this post, we will explore five critical questions that must be answered to achieve success. You can also use our Lead Screw Calculator Tools to quickly determine the best size lead screw for your application.
Lubrication
Proper lubrication is a must to achieve satisfactory service life when it comes to trapezoidal screws and assemblies. Although the actual means by which you deliver lubrication to the system and the specific lubrication intervals will vary from application to application, screw assemblies should be lubricated enough to maintain a film of lubricant on the screw. An exception to this general rule is when the assembly itself is self-lubricating.
Helix produces both "wet" and dry lubricants for our trapezoidal screw products. Helix PTFE dry coating is excellent for many applications such as food, medical, and semiconductor, where more conventional greases and oils are not desired. Our E-100 spray lubricant or our PAG-1 grease is recommended for applications using precision trapezoidal screws without PTFE coating.
Torque
The required motor torque to drive a trapezoidal screw assembly consists of three components: inertial torque, drag torque, and torque-to-move load. It must be noted that this is the torque necessary to drive the trapezoidal screw assembly alone. Due to general assembly misalignment, additional torque must also be considered when driving frictional bearings, motor shafts, moving components, and drag.
Tj = Iα
I = screw inertia
α = angular acceleration
TL = (Load x Lead) / (2Π x Efficiency)
Back Driving
Back driving is the ability of a screw to be turned by a thrust load applied to the nut. Generally, back driving will not occur when the screw lead is less than 1/3 of the diameter for uncoated screws, or 1/4 of the diameter for Helix PTFE coated screws. For higher leads where backdriving is likely, the torque required for holding a load is:
TL = (Load x Lead x Backdrive Efficiency) / (2Π)
Temperature
With proper lubrication, Helix trapezoidal screws with bronze nuts operate efficiently between 15°F and 350°F, and plastic nuts between 15°F and 175°F.
There you have it, four critical things to consider when using trapezoidal screws to drive your linear motion application. Determining these essential considerations of design will help to jumpstart your project in the direction of success.