What is a Stepper Motor?
A stepper motor is one of the most common motors used in motion control applications, primarily positioning applications.
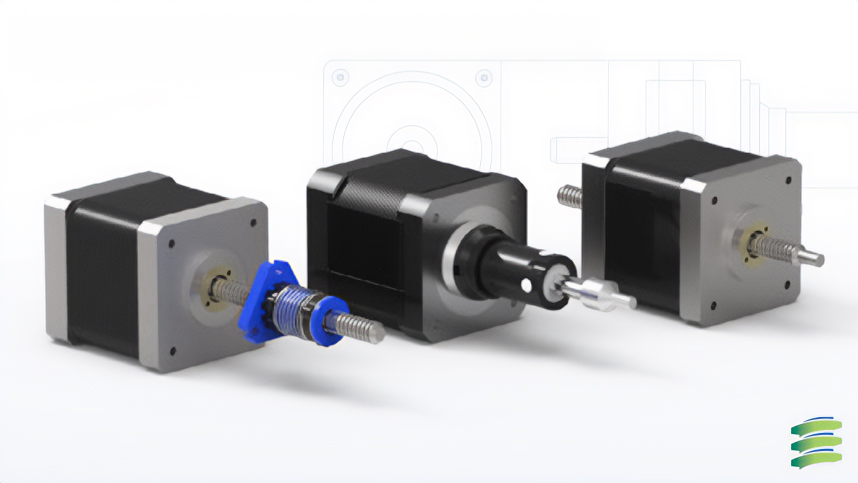
What is a Stepper Motor? A Comprehensive Guide
Stepper motors are a crucial component in the world of electronics, robotics, and industrial machinery. Known for their precise control, repeatability, and ability to maintain position without feedback, stepper motors are ideal for applications requiring meticulous accuracy. Let’s dive into what makes these motors unique, how they work, and why they’re widely used in various industries.
Understanding Stepper Motors
A stepper motor is an electromechanical device that converts electrical pulses into precise mechanical movement. Unlike a regular DC motor that spins continuously when power is applied, a stepper motor moves in discrete steps, typically a fraction of a degree. This design enables precise control over angular positioning, speed, and acceleration, making it ideal for applications where fine-grained control is required.
In a stepper motor, the movement is achieved by energizing coils in a specific sequence, causing the rotor to move incrementally. This controlled stepping allows for high levels of positional accuracy without requiring feedback systems, such as encoders, which are often necessary in other types of motors.
How Does a Stepper Motor Work?
Stepper motors operate based on electromagnetic principles. They typically consist of a rotor (the rotating part) and a stator (the stationary part). The stator contains coils, also known as windings, which are arranged in such a way that energizing them in a specific sequence causes the rotor to move by one step at a time.
Here’s a basic rundown of how stepper motors work:
1. Excitation of Coils: The stator has multiple coils that, when energized in a sequence, create magnetic fields that pull the rotor in small, incremental steps.
2. Incremental Movement: As each coil is energized, the rotor aligns itself with the magnetic field generated. By carefully controlling the order and timing of coil excitation, the rotor can be made to move in small steps, which are typically fractions of a degree.
3. Repeatable Positioning: Since each step corresponds to a known angular displacement, stepper motors offer repeatable positioning. This is a key advantage in applications that require accurate and repeatable motion control.
4. Open-Loop Operation: Stepper motors operate in an open-loop system, meaning they don’t need a feedback mechanism to verify the rotor’s position. As long as the motor does not miss steps, the controller can assume the rotor is in the desired position.
Types of Stepper Motors
There are several types of stepper motors, each with unique characteristics suited to different applications.
1. Permanent Magnet (PM) Stepper Motor: This motor uses permanent magnets for the rotor, which is attracted to the stator's electromagnetic poles. It typically has lower resolution but is efficient and cost-effective.
2. Variable Reluctance (VR) Stepper Motor: This motor doesn’t use magnets. Instead, the rotor is made of soft iron, and it moves based on the principle of minimum magnetic reluctance. This type has lower holding torque but is quick in response.
3. Hybrid Stepper Motor: A combination of PM and VR technologies, hybrid stepper motors offer high resolution and good holding torque, making them a popular choice in precision applications.
Advantages of Stepper Motors
Stepper motors have several advantages that make them a preferred choice in many applications:
- Precision Control: Each step moves the motor by a precise angle, allowing for accurate positioning without the need for feedback systems.
- High Torque at Low Speeds: Stepper motors can deliver high torque at low speeds, which is essential for applications requiring steady, slow movement.
- Reliability: With no brushes to wear out and an open-loop operation, stepper motors are known for their reliability in demanding environments.
- Repeatable Movements: The nature of stepper motors ensures that movements are repeatable, making them ideal for tasks requiring consistent positioning, such as in 3D printers or CNC machines.
Limitations of Stepper Motors
While stepper motors offer significant advantages, they do have some limitations:
- Lower Efficiency: Stepper motors can be less efficient than other motor types, particularly at high speeds. They tend to draw current continuously, even when stationary.
- Heat Generation: Continuous current flow through the windings can cause stepper motors to generate heat, which may be an issue in sensitive applications.
- Potential for Step Loss: Stepper motors may lose steps under heavy load or if they’re asked to move too quickly. This can lead to positional inaccuracies if not carefully controlled.
Applications of Stepper Motors
Stepper motors are employed in a variety of industries and applications due to their accuracy and reliability. Here are some typical applications:
1. 3D Printers: Stepper motors drive the precise movements required in 3D printing, allowing for fine resolution and repeatable positioning.
2. CNC Machines: In CNC (Computer Numerical Control) machines, stepper motors control the position of tools with precision, enabling automated cutting, drilling, and milling.
3. Robotics: Stepper motors are popular in robotics for their ability to offer precise control over motion, enabling robots to perform tasks like picking and placing.
4. Medical Equipment: Devices like MRI machines and surgical robots often use stepper motors for their reliability and high positional accuracy.
5. Cameras and Optical Equipment: Stepper motors control zoom, focus, and aperture in cameras and other optical equipment, where exact positioning is crucial.
Selecting a Stepper Motor for Your Application
Choosing the right stepper motor involves considering several factors:- Step Angle: This refers to the degree of rotation per step. Smaller step angles offer higher precision but may require more power.
- Torque Requirements: Stepper motors come in various torque ratings. It’s essential to select a motor that can handle the load without stalling or losing steps.
- Driver Compatibility: The motor driver is responsible for providing the correct sequence of electrical pulses to the stepper motor. Ensuring compatibility between the motor and driver is critical for efficient operation.
- Environmental Considerations: Certain applications may require motors that can withstand specific environmental conditions, such as high temperatures or moisture.
Commonly Used Stepper Motor Drivers
Stepper motors require drivers to manage the sequence of electrical pulses. Some commonly used stepper motor drivers include:
1. A4988 Driver: A widely-used driver in low-cost applications, it offers basic functionality and current control.
2. DRV8825 Driver: Known for higher current capacity, it’s used in applications that need more torque.
3. TB6600 Driver: This is a robust driver for high-torque applications, often used in CNC machines and large 3D printers.
Each driver has unique characteristics that affect the motor’s performance, so selecting the right driver is crucial for achieving optimal results.
Optimizing Stepper Motor Performance
To get the best performance from a stepper motor, consider these tips:
- Microstepping: Microstepping allows the motor to move in smaller increments, reducing resonance and increasing smoothness.
- Current Limiting: Proper current limiting prevents the motor from overheating and ensures longevity.
- Power Supply: Ensure that the motor’s power supply is adequate for the torque requirements, especially in high-load applications.
Stepper motors are invaluable in precision control applications due to their accuracy, repeatability, and reliability. They’re widely used in industries ranging from manufacturing to healthcare, providing reliable and controlled movement in countless devices. Understanding the fundamentals of stepper motors can help engineers select the right motor for their needs, optimize performance, and address limitations in specific applications.
Whether you're building a 3D printer, developing a robotic arm, or automating machinery, a stepper motor might be the perfect solution for achieving fine-grained control and dependable motion.
#steppermotor #precisioncontrol #motioncontrol #robotics #CNC #3Dprinting #automation #engineering #industrialautomation #machinery #motorcontrol #electronics #manufacturing #motortechnology #steppermotordrivers