How a Stepper Motor Actuator is Used for Linear Motion
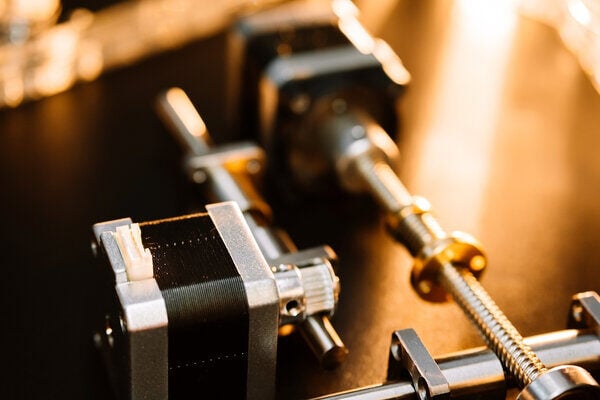
A stepper motor is an electro-mechanical device that transforms electrical energy into accurate and precise mechanical movement. This makes it extremely valuable for applications that demand precise positioning. Stepper motor actuators move in discrete, controlled steps, allowing for highly accurate motion without needing feedback systems. This step movement makes them valuable in the factory automation, robotics and the medical device industries. The motor must be correctly sized for the specific application to deliver reliable and repeatable performance, offering a powerful and straightforward solution for achieving accurate control.
How stepper motor actuators work
Stepper motors are operated using a stepper controller and driver. These parts send a sequence of electrical pulses to the motor. Each pulse corresponds to a specific step in the motor's rotation, making precise control over the motor's movement much more possible. This pre-programmed sequence ensures that the motor rotates accurately according to the application.
The pulses energize the motor's coils, generating magnetic fields that interact with the magnets attached to the rotor sections of the motor shaft. These interactions cause the rotor to turn in a series of controlled, stepwise motions, allowing the motor to position accurately.
Some key parameters are needed for stepper motor actuators to perform well. These are torque, speed, acceleration and resolution.
- Torque is the force that causes the motor to rotate, and it loosens or tightens the nut along the lead screw's axis, allowing precise linear motion.
- Speed refers to the rate at which the motor can rotate, directly impacting the resulting linear motion. Balancing speed and torque is crucial for optimal performance.
- Acceleration is the rate at which the motor can increase its speed from a standstill, which is important for applications that use rapid movement.
- Resolution determines the accuracy of the motor's steps. Higher resolution allows for finer control over positioning, making it ideal for applications that demand high accuracy.
How stepper motor actuators use linear motion
Linear motion is movement along a straight line from one point to another. This motion needs to be highly accurate in many applications, and this is where stepper motor actuators excel.
The rotational motion of a stepper motor is converted into linear motion through a lead screw. As the motor rotates the threaded lead screw, a nut attached to the load moves along the screw's axis, translating the rotational steps into linear displacement. This mechanism allows the actuator to attain highly accurate linear motion, making it ideal for error-free applications.
By understanding stepper motor actuators' fundamental parameters and mechanics, professionals can appreciate their essential role in delivering exact and repeatable linear motion across various high-precision applications.
At Helix Linear Technologies, we recognize the importance of high-performance stepper motor actuators in modern engineering. We offer various stepper motor actuators designed to suit diverse applications. Whether you need compact actuators for space-constrained environments or high-torque models for more demanding tasks, we offer solutions combining precision and reliability. Our commitment to quality ensures that our stepper motor actuators deliver consistent, repeatable results, making them the go-to choice for engineers who need dependable linear motion solutions.